Effective Application of Corrosion Inhibitors Under Changing Flow Conditions
The nature of the oil extraction process involves use of a myriad of reagents for the extraction process. These range from fracturing fluids, water, oxygen, brine and even hydrogen sulfide. When combined there occurs serious danger of corrosion and measures must be taken to reduce this corrosion. The rate of maturity and deterioration of pipelines is fast and continuous replacement of these installations is very costly. This has led to development of various corrosion inhibitors, and more research is being done in the improvement of the existing pipeline corrosion inhibitors.
Statistics on the Utilization of Corrosion Inhibitors
Under the current and existing corrosion management systems, over 3.7 billion dollars is spent per year to reduce the effect of corrosion in the oil production and refining industry. In an effort to bring this cost down there has been a tremendous effort by researchers to develop an optimal combination of flow enhancers and crude oil line corrosion inhibitors in order to increase protection of the surfaces.
This prolongs the life of the equipments and effectively reduces the cost of operation and maintenance.
Available Active Ingredients for Corrosion Management
Corrosion inhibitors are formulated with ingredients such as;
- Intermediate inhibitors
- Carboxylic acid
- Demulsifier or surfactant in an aromatic solvent
- Alcohol
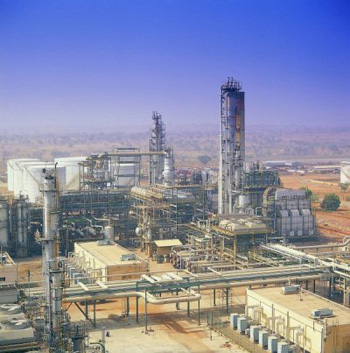
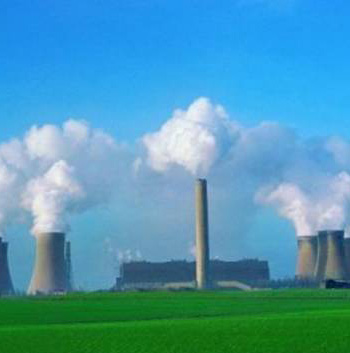
The intermediate inhibitor is the main active constituent in the inhibition process.90 % of all inhibitors used in the oil production process are nitrogen containing compounds. They are effective due to the 2 free electrons in the nitrogen atom. These are easily adsorbed to the metal surface and their hydrocarbon chain resulting in the formation of a hydrophobic film on the surface of the metal, creating inhibition.
Effect of Flow Enhancers in Pipeline Management
The management of corrosion is highly improved by the alteration of the flow properties of the crude. Gas oil corrosion inhibitors are combined with flow enhancing compounds simply called Drag Reducing agents (DRA’s)
Modification Effects of Combining Amine Inhibitors with Volatile Corrosion Inhibitors
New research has led to the development of volatile corrosion inhibitors (VpCL’s) which when combined with the amine based inhibitors, offer greater protection on the steel surfaces. They work by creating a self regenerating mono molecular layer on the surface giving great protection against carbon dioxide, hydrogen sulfide, oxygen and other corrosive contaminants
Drag Reducing Effects of Various Active Ingredients
Research shows that drag reducing compounds combined with oxidation inhibitors produce to better performance in corrosion inhibition. Drag reducers bring down frictional pressure which occurs during the turbulent flow of crude inside the pipe. They are therefore wonderful combinations when used with oil pipeline corrosion inhibitors.
Ongoing Research on Modification of Oxidizing Chemicals
Research on the inhibitor performance is still ongoing. Areas of focus include evaluation of inhibitor performance at high pressure and temperature (the high pressure wheel test); the “continuous wheel test” method is also designed to simulate ongoing crude treatment in the field.
Conclusion
Development of different combinations of pipeline gas and water corrosion inhibitors and modifying agents has led to good reduction in the operating pressure of the pumping systems as well as longer lasting infrastructure. This has ultimately led to improved oil production and increased revenue.
This article has been written by Govind Patel.